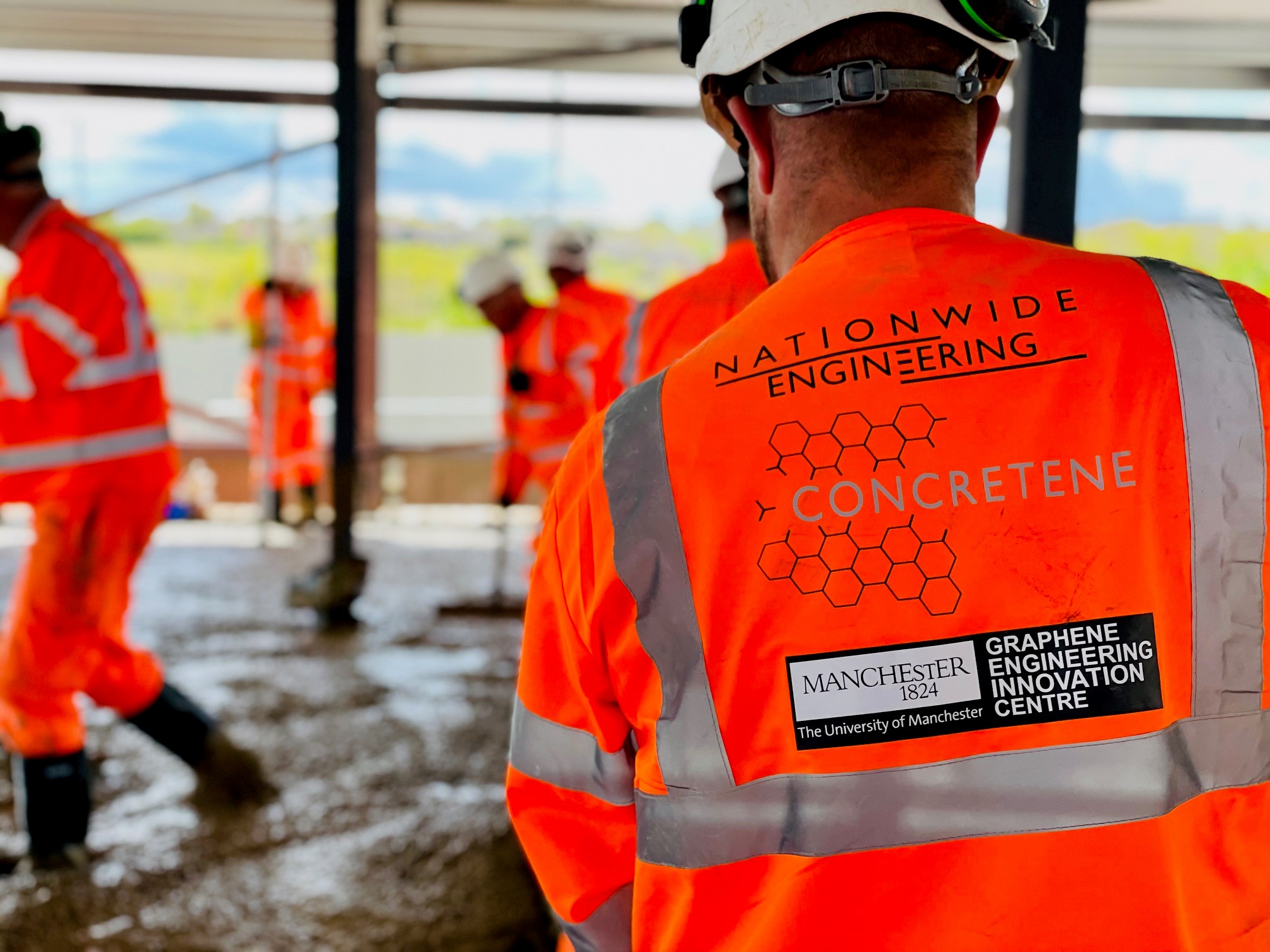
Graphene Concrete: Making Building Greener and Cheaper
Manchester
Our Story
The journey to reduce our carbon and environmental impact started when we began recycling 100% post-industrial plastic and products that didn’t meet QC standards. Transferring out waste to a recycling centre, it is processed (along with material from other companies) to create our Wham Barn material, which we then mould to manufacture boxes. By repeating this process, we realised the true potential value in our waste.
Our initiative to manufacture and introduce upcycled products to our range started in early 2018. Following a ban on importing plastic from China, the UK had a void in terms of a sustainable solution to single-use plastic waste, with most either being sent to landfill or the incinerator. Responding to this change in policy, we worked directly with recyclers and material scientists to trial and develop a process which was commercially viable.
Using more upcycled and recycled materials has allowed us to offer an ever-expanding range of products to our customers that have a much lower carbon and environmental impact. With the help of our suppliers and team we can continue to expand our production and contribute towards a circular plastics economy with a smaller carbon footprint.
The Challenge
Engaging with local communities and business groups was paramount to the projects success. This gave us a valuable insight into what works, what people want and how we could achieve our goals. Moreover, it helped spread a positive message and gained traction and support for our project by engaging with local groups. There is often a misconception among communities about plastic so it was important for us to educate people on this, and it proved to be a successful way of mobilising support for our wide range of upcycled and recycled products.
Many people simply didn’t understand the difference between our plastic and a throwaway plastic bottle. By engaging people on the difference between the lifecycles of the two groups of plastics, we have gained enormous traction which is partly demonstrated by our huge increase in production of recycled and upcycled products.
Research is another key thing to consider with a project like this; specifically what’s been done before, what’s been unsuccessful, and what hasn’t been tried before helped direct our project. Once our concept was nailed down, finding the best people for the job to refine and streamline the process was key and helped achieve the best result for our products.
By understanding the true extent of the problem we were aiming to address, it helped us find the best solution. We measured every parameter possible, and enabled us to gain a better pictured of the issue we were tackling. In our case it was measuring scrap output, supply of external recyclables, GHG emissions, production capacity of recyclers, and our own manufacturing processes.
Our Solution
The need to develop this project was twofold. Firstly, we wanted to innovate by transforming what others consider waste into valuable products, contributing towards the circular economy and putting less pressure on limited resources. Every tonne of up/recycled material we process into durable, long lasting boxes is a tonne of plastic not dumped on a landfill site or incinerated.
We estimate that the CO2 emissions from producing up/recycled material are between 6 – 7.5 times less than virgin material – which is a huge positive. By using these materials, we effectively eliminate 63% of the CO2 emissions related to the entire plastic value chain – from the initial production phase of plastic. Secondly we understand the growing concern around sustainability and we felt it was our responsibility as a plastics manufacturer to provide our customers a solution made out of the problem.
In total, we reckon that 4,068 tonnes of CO2 in the global plastic value chain could be offset by using recycled material. We are proud that our range or products has now expanded to over 100 products. With help from our suppliers and our team, we can continue to expand our production and contribute towards a circular plastics economy with a smaller carbon footprint.
FOR FURTHER INFORMATION CLICK HERE.
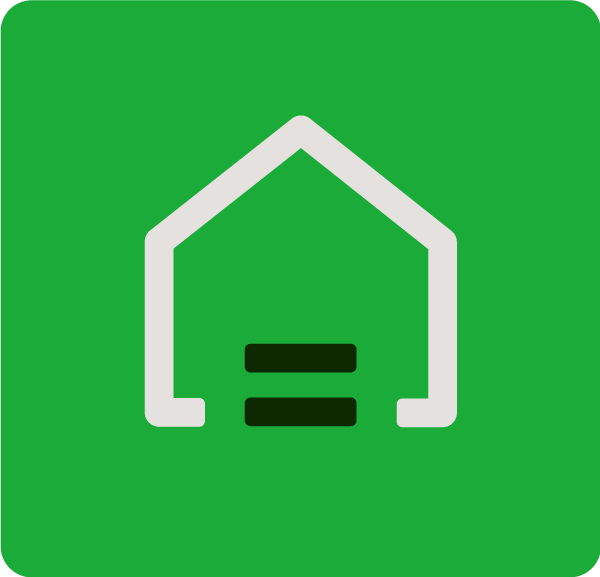